304: ist ein Allzweck-Edelstahl, der häufig bei der Herstellung von Geräten und Teilen verwendet wird, die eine gute Kombination von Eigenschaften (Korrosionsbeständigkeit und Formbarkeit) erfordern.
301: Edelstahl zeigt während der Verformung ein offensichtliches Phänomen der Kaltverfestigung und wird in verschiedenen Fällen verwendet, bei denen eine höhere Festigkeit erforderlich ist.
302: Edelstahl ist im Wesentlichen eine Variante von Edelstahl 304 mit höherem Kohlenstoffgehalt und kann für eine höhere Festigkeit durch Kaltwalzen hergestellt werden.
302B: Es handelt sich um einen Edelstahl mit hohem Siliziumgehalt und hoher Oxidationsbeständigkeit bei hohen Temperaturen.
303 und 303SE: Automatenedelstähle mit Schwefel bzw. Selen für Anwendungen, die Automatismus und hohe Lichthelligkeit erfordern.Edelstahl 303SE wird aufgrund seiner guten Warmumformbarkeit unter solchen Bedingungen auch für Teile verwendet, die Warmstauchen erfordern.

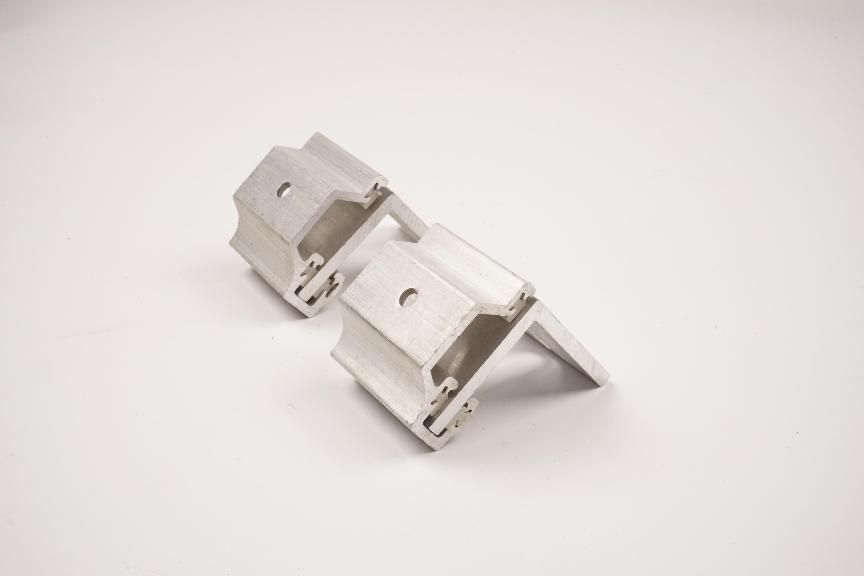
304L: Eine Variante des Edelstahls 304 mit einem geringeren Kohlenstoffgehalt für Schweißanwendungen.Der geringere Kohlenstoffgehalt minimiert die Karbidausfällung in der Wärmeeinflusszone nahe der Schweißnaht, was in manchen Fällen zu einer interkristallinen Korrosionsumgebung (Schweißangriff) bei rostfreiem Stahl führen kann.
04N: Es handelt sich um einen stickstoffhaltigen Edelstahl.Um die Festigkeit des Stahls zu verbessern, wird Stickstoff zugesetzt.
305 und 384: Edelstahl hat einen hohen Nickelgehalt und eine niedrige Kaltverfestigungsrate und eignet sich für verschiedene Gelegenheiten mit hohen Anforderungen an die Kaltumformung.
308: Edelstahl wird zur Herstellung von Elektroden verwendet.
309, 310, 314 und 330: Der hohe Nickel- und Chromgehalt von Edelstahl erhöht die Oxidationsbeständigkeit und Kriechfestigkeit des Stahls bei erhöhten Temperaturen.Während 30S5 und 310S Varianten von Edelstahl 309 und 310 sind, besteht der einzige Unterschied im geringeren Kohlenstoffgehalt, der die Karbidausfällung in der Nähe der Schweißnaht minimiert.Edelstahl 330 weist eine besonders hohe Beständigkeit gegen Aufkohlung und Thermoschock auf.
Typen 316 und 317: Edelstahl enthält Aluminium, sodass seine Beständigkeit gegen Lochfraß in Meeres- und Chemieindustrieumgebungen viel besser ist als die von Edelstahl 304.Zu den Sorten des Edelstahls 316 gehören der kohlenstoffarme Edelstahl 316L, der stickstoffhaltige hochfeste Edelstahl 316N und der hochzerspanbare Edelstahl 316F mit Schwefelgehalt.
321, 347 und 348 sind mit Titan, Niob bzw. Tantal und Niob stabilisierte Edelstähle.Sie sind zum Hochtemperaturlöten geeignet.348 ist ein Edelstahl, der für die Kernenergieindustrie geeignet ist.Die Tantalmenge und die Anzahl der Bohrlöcher sind begrenzt.
Die Induktionsspule und der mit der Schweißzange verbundene Teil sollten sicher platziert werden, um zu verhindern, dass der Lichtbogen während des Betriebs auf das Stahlrohr trifft.
Zeitpunkt der Veröffentlichung: 03.06.2019